Phillips Slot Combination Screw
What are Phillips and Pozi Heads?
A screw is defined by the presence of a drive manufactured into its head. Phillips and Pozi drives are two of the most widely-used drive types in the world - their names may be different, but they share many similarities, and both designs were originally created by the Phillips Screw Company. There are several important differences between the two drive types:
Combination Slotted/Phillips Machine Screws. Machine screws are used to secure panels and parts through existing, tapped holes on electronic equipment, engines, and large machines. Fillister and cheese head screws have deep slots to allow increased driving power. Flat head machine screws lie flush with the material surface. Standard Phillips and Torx® recesses as well as combination recesses available Screw head doubles as knob for hand actuation Stylized knob for hand actuation, and ratchet-mechanism or smooth knobs for restricted access Spring ejected design retracts threads when not engaged. Combination Dual Material Screwdriver Set 80050 Item No. Description 80015 1/8' x 3' Slotted Screwdriver 80013 1/4' x 4' Slotted Screwdriver 80023 5/16' x 6' Slotted Screwdriver 80022 3/8' x 8' Slotted Screwdriver 80001 #1 x 3' Phillips Screwdriver 80007 #2 x 4' Phillips Screwdriver GearWrench KD 80050 6 Pc.
16Pc Slotted/Phillips Ergonomic Professional Combination Screwdriver Set Fastenal Part No. Material: Steel Finish: Natural Color/Appearance: Bright Knob Style: Knurled Knob Material: Aluminum Alloy Thread or Hole Type: 10-32 Head Style: Phillips/Slot Combination Installation: Flare-in Recess Size: Phillips #2/Slot Combination Series: Styled Knob Min. Outer Panel Thickness (mm): 4.80 Max Outer Panel Thickness (mm): 6.40 Fastened Screw Projection (mm): 11.1000 Unfastened Screw.
Head Type | Slotted Head | Phillips Head | Pozi Head |
---|---|---|---|
When was it invented? | Invented pre-1600 | Invented 1934 | Invented 1959 |
Why was it invented? | Basic drive | Improvement upon slotted drive | Improvement upon Phillips drive |
What is the drive shape? | One slot | Four radial slots | Eight radial slots |
How is it located? | Manual alignment | Self-centralising | Self-centralising |
Will it cam-out? | Susceptible to cam-out | Slight resistance to cam-out | Improved resistance to cam-out |
What is the tip shape? | Flat tip | Angular tip | Shallow angular tip |
How many flutes? | No Flutes | Tapered flutes | Parallel flutes |
How is it manufactured? | Manufactured by broaching | Manufactured by punch | Manufactured by punch, and resistant to metal fall-away |
For a broader comparison of drive types, and information on further drive developments such as Pozidriv vs Torx, see our article, What is The Best Screw Drive?. A full summary of the advantages and disadvantages of Phillips and Pozidriv fasteners can be found below:
The Phillips Drive
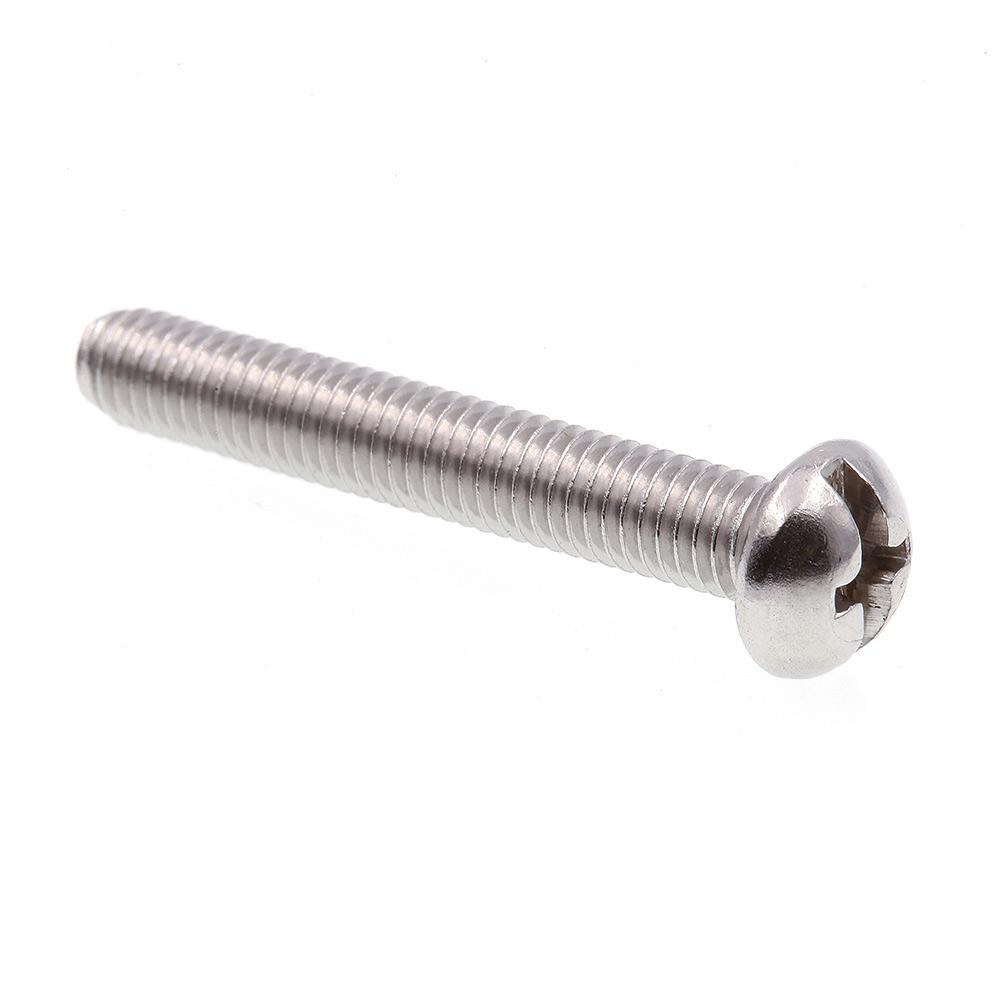
- Patented in 1936
- An improvement upon slotted drives
- Reduction in cam-out
- Tapered flutes
- Manufactured by punching
Introduced as an improvement on the widely-used flat head drive, the Phillips drive, invented by Portland mechanic John Thompson but named for its legal owner, Henry Phillips, was one of the first attempts to improve upon the basic, yet flawed, flat head formula. Slotted drives were used in the vast majority of contemporary screw designs, but tended to slip from the open ends during installation, were difficult to align, and the slot required a closely matching bit to install. The cruciform design of the Phillips drive attempted to remedy these issues.
Phillips Sizing
One notable advantage of the Phillips drive over slotted drives is that Phillips recesses are manufactured according to a specified selection of sizes. Slotted drives are largely defined by the fastener head width. There is no defined slotted width for each fastener, and the most reliable selection criteria is to simply choose the largest possible screwdriver to maximise leverage, without the driver protruding beyond the diameter of the screw head.
Phillips drives, on the other hand, require a significantly reduced number of permutations. The 1936 Phillips patent states that only two sizes of Phillips driver are required for screw sizes from number 5 to number 16. By contrast, a slotted drive would require 'six or more' sizes of screwdriver for the same size range.
Self-Centring Design
The Phillips Drive was devised to create a self-centring cruciform drive with four-way symmetry, meaning it required significantly less manual alignment to use, and supported the contemporary industrial shift towards mass production lines. Phillips’ keenness for his design to be considered for its exceptional compatibility with production lines and automated tooling can be seen in the wording of the patent itself, which states that the Phillips drive is “highly advantageous in presenting screws to be driven, either by hand or by power-driven types of tool”.
Susceptibility to Cam-Out
The creation of a cruciform drive provided better engagement with driver, and reduced the chance of accidental slippage when compared to the more unstable slotted alternative. This effect is widely known as “cam-out”. Interestingly, though Phillips drives are definitely advantageous in reducing the chance of cam-out compared to slotted drives, the earliest Phillips drive patent makes no reference to the phenomenon of cam-out - only in a later submission does Henry Phillips mention the effect, claiming that cam-out should be avoided, and is “not only dangerous to the operator, but is likewise, always injurious to the work”.
The Downside of Tapered Flutes
The Phillips drive is designed with curved edges on each of its four wings to guide the driver into the drive. The disadvantage of using a drive with such curvilinear recesses is that the gentle slope encourages the driver to disengage at high torque. This issue was improved upon with the later development of the Pozi drive.
The Advantage of Punched Drives
The manufacture of Phillips drives also embraced the use of mechanised drive punches rather than more traditional machined drives; this promoted efficient fastener production and took full advantage of mechanised production lines of the early 20th century. The creation of a stamped recess also allows the driver to match perfectly with the drive. The drive is pressed into the screw by a die which matched the exact dimensions of the driver, unlike alternative methods of the time, such as broaching, which would simply cut the general shape of the tool into the top of a screw. Henry Phillips’ original patent specifically mentions that the common broached drives of the time could never match the mating accuracy of a stamped Phillips drive.
Fastener Retention
As an additional bonus, the Phillips drive improved upon slotted drive by providing some degree of fastener retention when a screw came into contact with the driver. The original patent for the Phillips drive states that “a screw may be first secured to the end of a driver, and presented to the work to be dealt with without the inconvenience of the screw dropping from the end of the driver.” The 1934 patent also argues that this design allows fasteners to be installed with one hand, a relatively innovative feature which may now be taken for granted.
The Pozi Drive
- Patented in 1963
- Improvement upon Phillips drives
- Further reduction in cam-out
- Parallel flutes
- Improved manufacture by punching
The Pozi drive, often known by its trade name, Pozidriv, or misspelled as Posi, Posidriv, or Posidrive, was patented in 1963 as an improvement upon the Phillips Drive, which was, itself, an improvement upon the archaic slotted recess. Arguably, the most significant and visually obvious feature of the Pozi drive is the addition of four equiangular, equidistant “wings” incorporated into the original cruciform design, but several other features, including a redesigned head shape, give the Pozi the edge over Phillips drives in many applications.
Pozi Sizing
Like the Phillips drive before it, the Pozi drive is defined by a small number of regimented sizes. Pozi heads are available in ascending sizes of 0, 1, 2, 3, 4, and 5. Pozi sizes can be expressed in several different ways, such as the abbreviation PZ, or simply a 'number' size - this, coupled with the non-standard spelling of the brand name 'Pozidriv', can lead to confusion in definition. For instance, the terms pozidrive PZ2, Pozidriv #2, or posidrive no. 2 can all refer to the same size of drive.
Increased Torque Capacity
One of the primary optimisations of the Pozi drive was in its improved ability to be used in self-tapping applications, which require significantly increased torque to drive the screw into an unprepared hole. The previous Phillips drive performed poorly in high-torque applications, and was plagued by cam-out, despite its supposed improvements over the slotted drive.
One solution to this issue would be to use one of the newly-invented deep socket-type drives such as the Robertson drive, but with head-shapes such as those found on countersunk screws, deep-sided sockets could get dangerously close to the countersunk outer edge of the head, potentially causing structural weakness - in these applications, an angular drive such as Phillips or Pozi may be a superior option. Although Pozi drives were developed with countersunk heads in mind, they are now more widely manufactured into pan head screws.
The addition of the Pozi drives’s radial notches created a greater number of contact areas between the fastener recess and the driving tool, which improved torque transmission and reduced the chance of slippage, allowing a shallow angular drive to compete with deeper sockets in terms of torque transmission.
Improved Stability
The Pozi drive’s design was not solely intended for high-torque applications, it was also intended to improve stability reduce cam-out in general. One additional improvement of the Pozi drive is the use of parallel flutes on the tip of the driver. The previous Phillips design used tapered flutes, which had a tendency to encourage disengagement due to their sloped shape. Parallel flutes provide a better ‘locking’ functionality, and discourage disengagement from the driver.
Improved Punched Drive and Metal Fall-Away
The punched drive of a Pozi fastener is specifically invented to combat a phenomenon known as “metal fall-away”, a common issues with the contemporary manufacture of punched drives which is somewhat unavoidable, but is particularly common in countersunk heads. The phenomenon known as metal fall-away is specifically mentioned numerous times within the original patent for the Pozi drive, and is a clear focus of the design. Metal fall-away is caused by the combination of “plowing”, the act of directly displacing material as the drive is formed, and “pullaway”, an effect caused by the removal of the die, where displaced material distorts in an effect roughly similar to water surface tension. The result of metal fall-away is that heads can be become distorted, creating a bulging head and loosely-fitting drive.
The original patent for the Pozi drive states that it combats the issue of metal fall-away by “providing a recess in which the ratio of the radial extent of the grooves to the central recess portion is reduced by providing, between each pair of adjacent grooves, one or more valleys or serrations in place of the conventional angular or curved rib or ridge.” - put simply, the Pozi drive creates a slightly more complex drive with a greater number of less severe indentations, which reduces the aggression of material displacement, and results in less deformation to the screw head during manufacture.
No Slot Screws
Can a Phillips Head drive a Pozi Screw?
Though often not recommended, there is some degree of cross-compatibility between a Phillips and a Pozi drive. Confusion between the Phillips and Pozi drives can cause significant damage during installation, however, Phillips and Pozi drives are structurally very similar, with both being heavily defined by their dominantly cruciform designs. This means that a Phillips driver can fit within the cruciform recess of a Pozi drive. However, the Pozi driver, with the addition of its four radial wings, cannot fit within the recess of a Phillips drive.
Machine Screw Wood Screw Combination
Interestingly, there is also some seemingly deliberate cross-compatibility between the Phillips or Pozi drives and a flat head screwdriver. Henry Phillips’ original patent for the Phillips drive describes its grooves as “diametrically opposed, to receive the ordinary fiat blade-driver such as is now commonly known and used.” As the Pozi drive features very similar diametrically opposed cruciform grooves, it can be assumed that similar compatibility can be expected from Pozi fasteners, though the efficiency and safety of this method is questionable, and generally not recommended.